Why Patient Engagement is Critical to Manufacturing & Supply
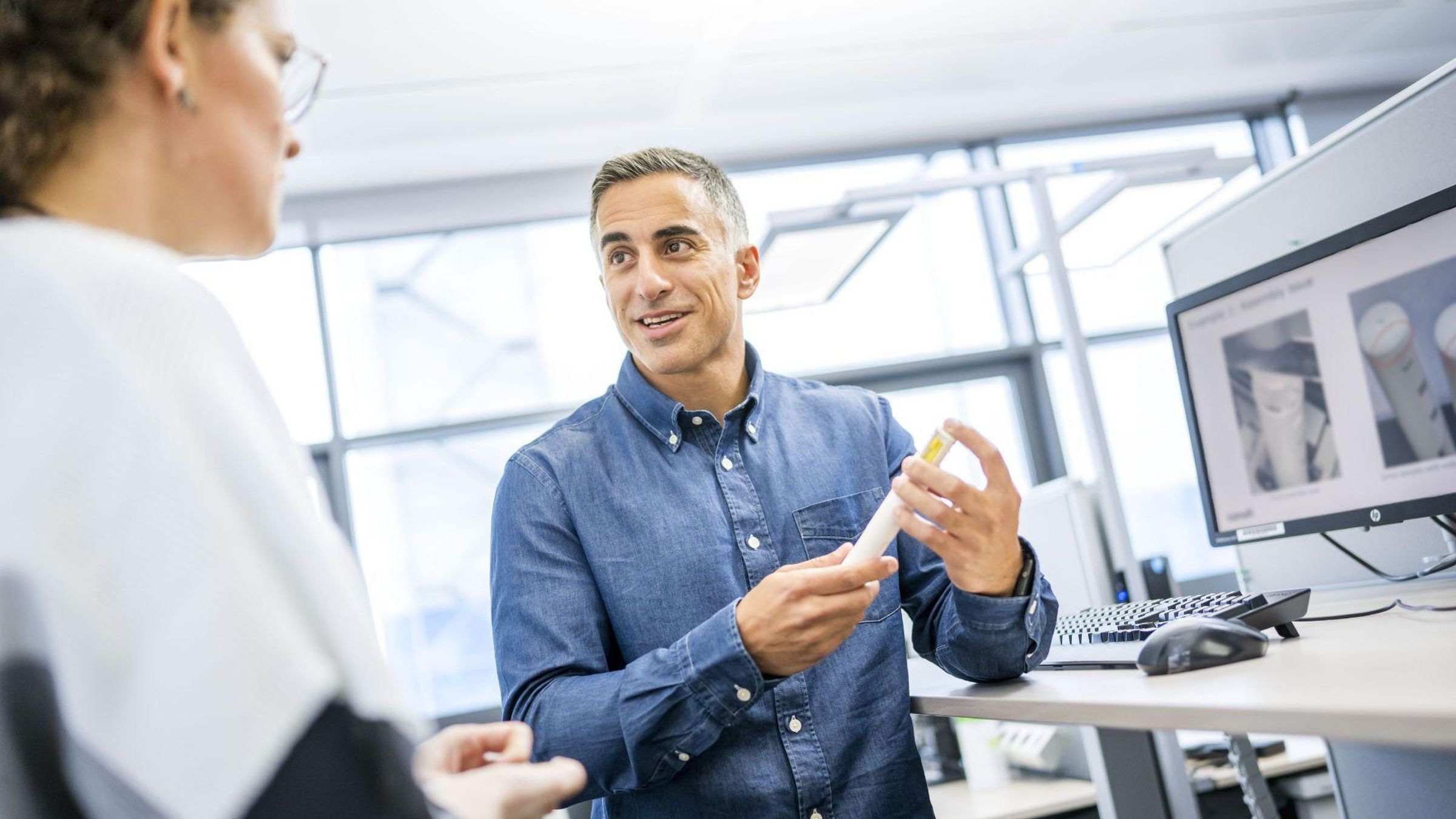
“Many years ago, my father was hospitalized for surgery, and while visiting him, I saw him being treated with a medical device that my team and I had directly developed and launched. I watched with a sense of gratification as the nurse used that product to flush my father’s catheter to maintain patency. Since then, my job has been deeply personal for me.”
Mitali Aon, SVP and Global Head of Device & Packaging, shares why and how the patient voice is so important to Manufacturing & Supply.
Integrated Engagement to Understand Patient Needs
Sanofi's mission is to transform the practice of medicine through breakthrough science and first/best-in-class medicines that address the clinical unmet need and some of the world’s most challenging health problems. To amplify that impact, we must also consider how our patients are likely to use and experience our products. Studies show that only ~50% of patients with chronic conditions regularly take their medications as prescribed.
Integrated patient engagement is about working with patients (not just for patients) to understand their needs in order to develop solutions that address this adherence gap. As healthcare systems evolve at pace, patients are an increasingly influential stakeholder we must engage with. At Sanofi, our Integrated Patient Engagement Program drives us to collaborate with patients at every stage of development, ensuring we fully deliver on the promise of our pipeline. This commitment includes engaging with global patient and health communities as well as patient advocacy groups, to support programs that help drive access to medicines and overcome barriers to treatment.
We don’t just design for patients, we design with patients. Manufacturing & Supply is uniquely positioned to ensure the patient experience is factored into our development processes, right from the earliest stages of clinical development.

Mitali Aon
SVP and Global Head of Device & Packaging
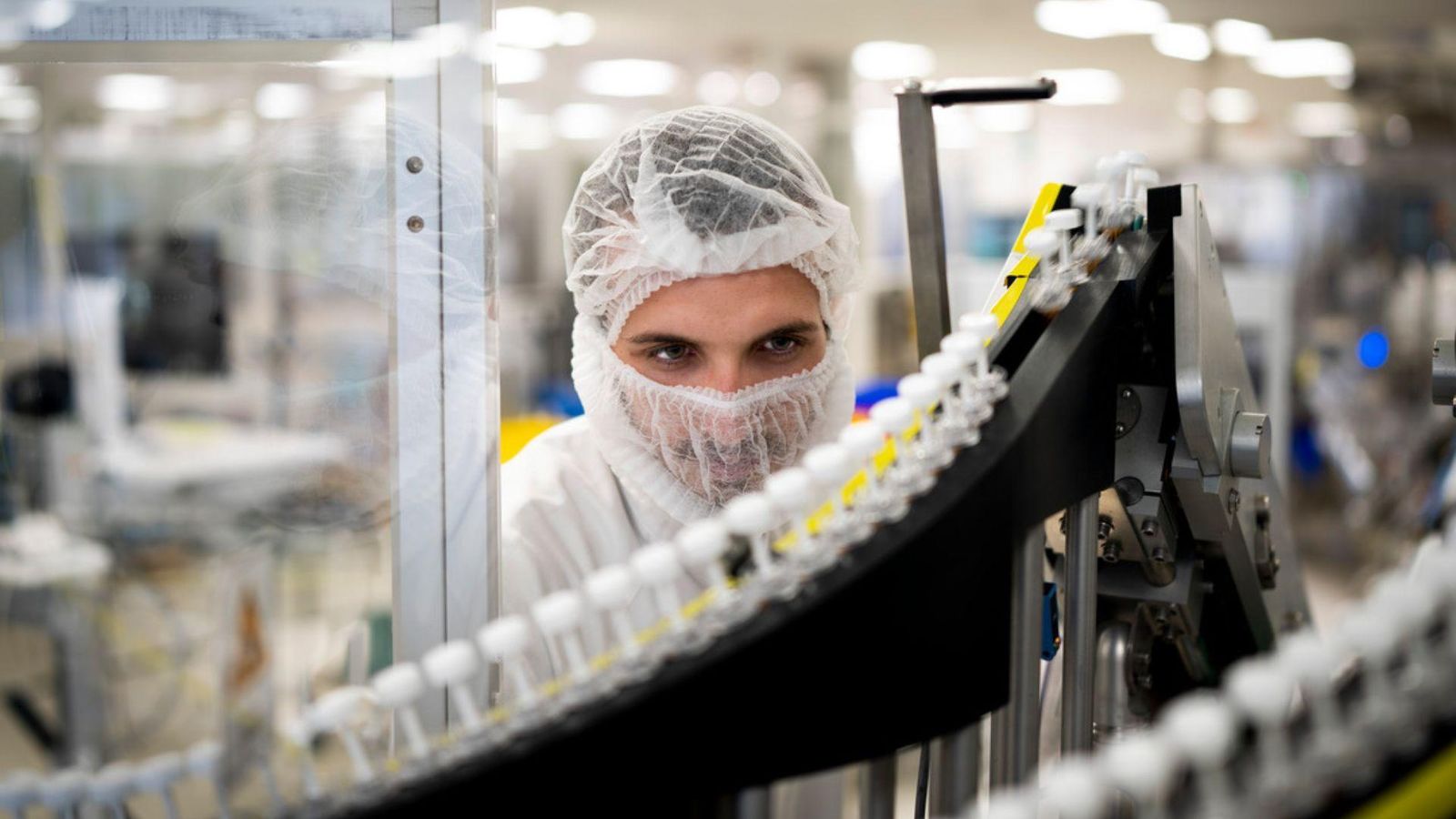
It’s important to remember that the ultimate customer is the patient. “We don’t just design for patients, we design with patients” is the mantra we embrace during our development process. Each touchpoint in the patient journey is an opportunity to gain deeper insights and shape that patient experience. In Manufacturing & Supply, we are uniquely positioned to ensure these insights are factored into our device designs, right from the earliest stages of development.
Engagement for Better Outcomes
A good example of our commitment to patient engagement was the development of one of our auto-injectors (pens) that was specifically designed for patients with rheumatoid arthritis (RA). RA significantly impacts manual dexterity due to joint pain and inflammation. Over time, it can lead to joint deformities, making it difficult to perform daily tasks due to decreased strength and range of motion. For patients having to self-inject every two weeks, this can make using a pre-filled syringe or pen very challenging. Therefore, our team devoted significant effort researching and gathering patient insights around the specific use challenges. Through this work, it was clear that patients struggled with firmly gripping the pen, hyper-extending the thumb to press the activation button, and/or holding down the pen for the entire duration of the injection. By collaborating with the patient community through human factors formative studies, we were able to jointly design a device that addressed these challenges: a button-less pen with low hold force and an ergonomic grip that feels comfortable/secure in the palm of the hands. In addition to receiving the RA Foundation’s seal of approval, this pen had a 98% patient satisfaction rate, fully delivering on the medicines’ therapeutic promise. Fundamentally, if we can positively influence the patient experience, we can help increase adherence, which ensures that the efficacy observed in clinical trials translates into real-world benefit.
An additional focus area for our team is environmental sustainability. Patients are also increasingly aware of the impact of the products they use on the environment. Hence, our team is equally focused on developing devices that minimize our impact to the environment to the extent possible. Using greener materials or enabling take-back programs allows products to be broken down into their component parts and further encourages recycling or repurposing for other non-healthcare uses.
We can only do this by shifting our thinking from patient centricity to patient integration: a relationship of transparency and trust, as well as an acknowledgement that the patient is the expert in their condition.
Mitali Aon
SVP and Global Head of Device & Packaging
Continuous Engagement for Continuous Innovation
Innovation is not just about the therapy itself – in Manufacturing & Supply, it means challenging ourselves to think differently about design and delivery, to take time to uncover what patients need and be bold in creating solutions. It means asking questions like: can we make this easier to administer, can we reduce the burden of treatment, and can we provide additional information and guidance through digital channels to give patients more control into their treatment and ultimately upskill their self-management? We can only do this by shifting our thinking from patient centricity to patient integration: a relationship of transparency and trust, as well as an acknowledgement that the patient is the expert in their condition.
Although we are proud to be recognized for our approach to product design and have received multiple awards for our commitment to excellence in patient care, the most important metric of success is being able to contribute to a positive patient experience and ultimately improve health outcomes for the patients we serve. That’s the goal we strive for.
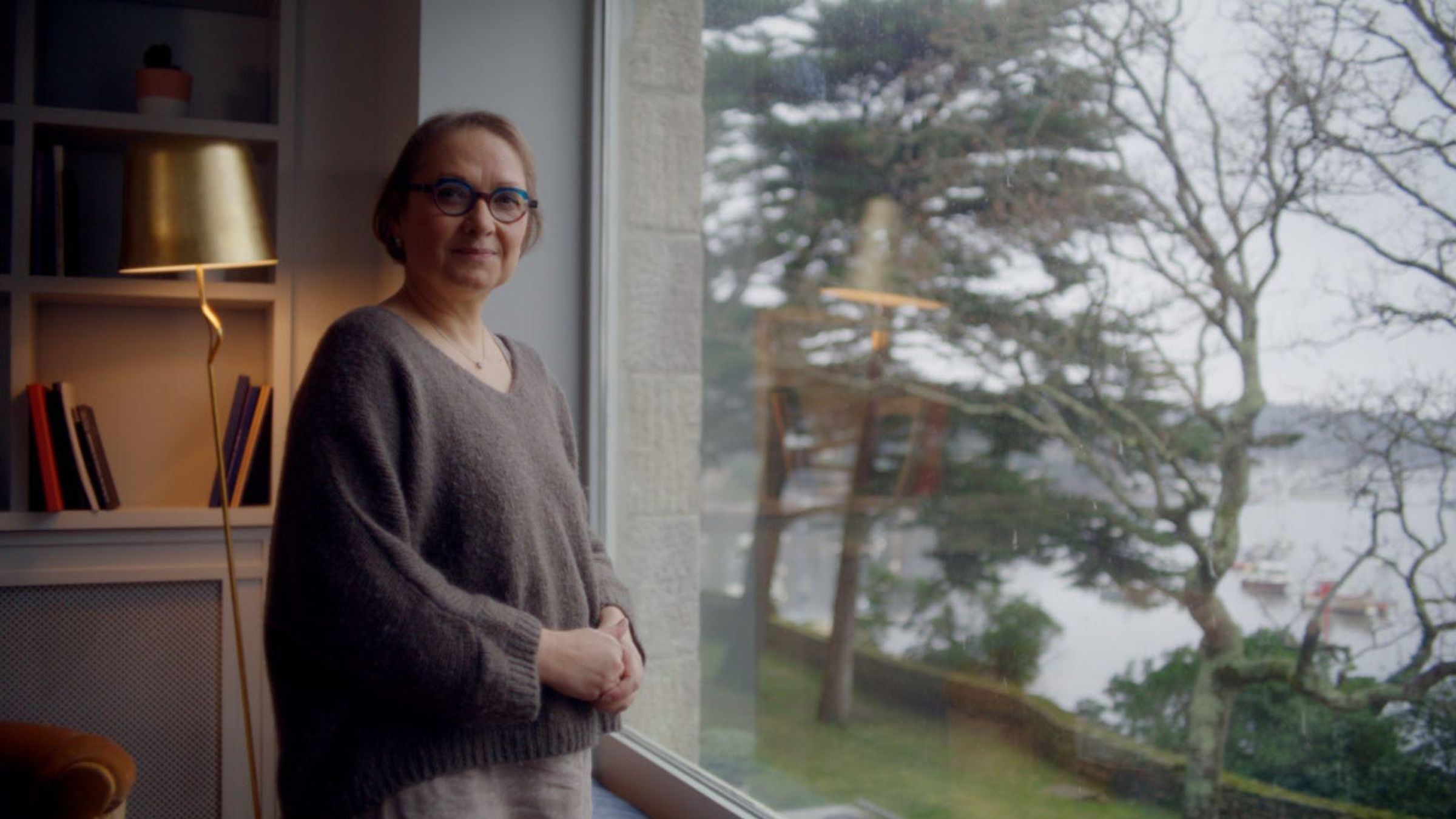
References
- Haynes RB, McDonald HP, Garg AX. Helping patients follow prescribed treatment: Clinical applications. JAMA. 2002;288(22):2880-2883.